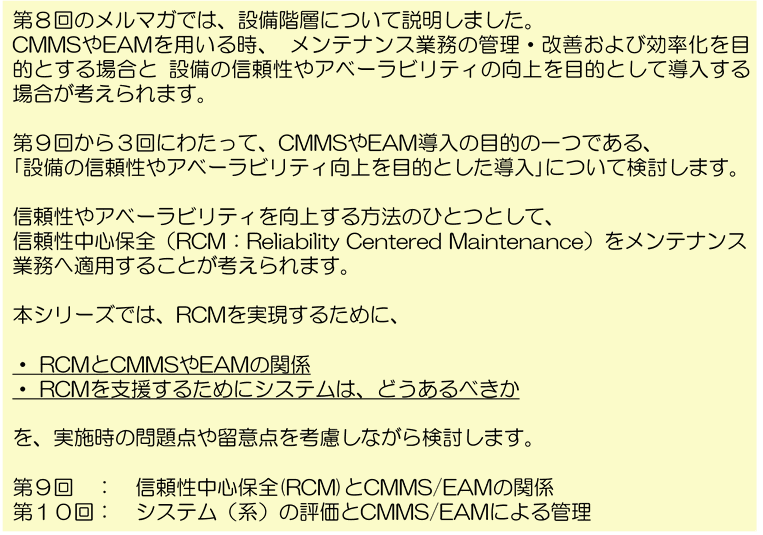
1.信頼性中心保全(RCM:Reliability Centered Maintenance)
1960年代から70年初頭にかけて、航空業界では、 航空機の大型化と複雑化、それに伴う整
備コストの増大に悩まされ、 「その、メンテナンスは、本当に必要なのか」、 「信頼性の確保は
大丈夫か」という観点から、 新しいメンテナンス方式の確立に迫られていました。
このことを受け、航空輸送協会(ATA)は、 1968年に新しいメンテナンス方式を発表しまし
た。 これは、後にMSG-1と呼ばれています。MSG-1は、1970年にMSG-2へ、 更に
1980年にMSG-3として見直しが行われました。
1970年代半ばには、米国国防総省(DoD)においても、 航空業界でのメンテナンス方式を
参考に、 検討が進められ、1978年に「RELIABILITY-CENTERD MAINTENANCE」を冠し
た レポートが発表されました(※1)。
80年代には、原子力の分野でも、米国電力研究所(EPRI)を 中心に発電所への適用が検討さ
れ始めました。
※1 補足説明:
本レポートは、ユナイテッドエアラインの Stanley NowlanとHoward Heapによ
ってまとめられ、 航空機以外の分野への適用についても言及しています。
2.故障特性
Nowlan&Heapの報告書では、故障特性に関する記述が盛込まれました。 本故障特性は、こ
れ以後、機器の故障特性の説明やRCMの有効性の説明に、 色々な分野で参照されています。
また、後続のRCM関連レポートでは、本故障特性ごとに分布を求めたものが いくつか存在し
ます。以下に、本故障特性を示します。
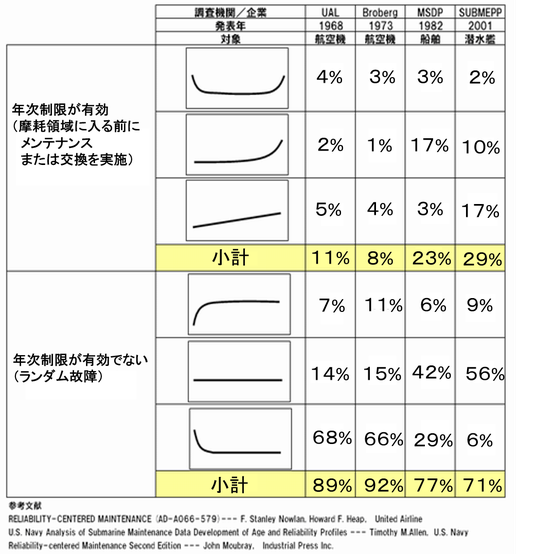
図1 6つの故障特性
上図は、故障率のパターン(故障特性)ごとにその割合をまとめたものです。
上図は、摩耗故障領域を有するアイテムのように、耐用年数を考慮して定期的に(摩耗故障に
至る前に)メンテナンスや交換を実施することで寿命を延長できるアイテムが少ないことを示
しています。(30%以下)(※2)。 すなわち、時間基準保全(TBM)が有効なアイテ
ム数が少ないことを示しています。
また、初期不良が発生するアイテムの数も多いため、 過剰なメンテナンスに対する留意が必
要であることを示しています。
他は、ランダム故障の特性を示します。 ランダム故障を示すアイテムに対しては、状態監視
による状態基準保全(CBM)や 検査結果に基づく寿命予測などによる計画が重要になります
(※2)。
※2 補足説明:
アイテム単体の故障モードごとに故障率パターンが既知であったとしても、それらを
組み合わせて提供する機能(システムやユニット)は、いろいろな故障モードが重な
り、全体としては、ランダム故障の特性を示す場合があることが知られています。
言い換えるとどの粒度で観測するかにより故障率のパターンは変わります。
3.実施内容
RCMは、信頼性や保全に対する戦略の立て方に対する指針を示したものであり、 対象設備や
装置、システムに対する検査の方法や維持管理の手法を 示すものではありません。 よって、
アイテムの故障モードやシステムへの影響を検討するためには、 対象設備の専門化、ベンダ
ー、オペレータなどが参画する必要があります。
RCMでは、アイテムの故障特性を考慮し、 どの様なメンテナンス方式を採用するかについて
デシジョンツリー (考え方のテンプレート)を用いて判断します。 以下に例を示します。
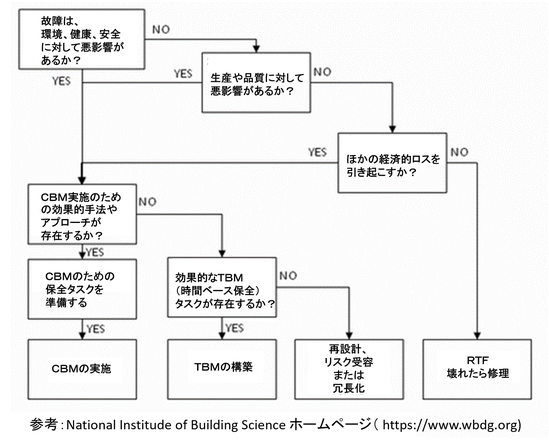
図2 デシジョンツリーの例
ここで、重要なことは、着目するアイテムに対して
・どの様な故障(故障モード)が存在するのか
・故障が、システムに対してどの様な影響を与えるのか
・その影響により、どの様な被害を被るのか、
・そして、その故障は、どれくらいの頻度で発生するのか(起こりやすさはどれくらいか)
を把握、整理し、
・被害の大きさと起こりやすさからリスクを検討し、
・許容できるリスクなのか、許容できないとしたら、
・リスクの排除や軽減(影響を軽減する又は起こりやすさを小さくする)するための方法が
存在するか
・方法が存在しない(制御できない)としたら、制御できるよう設計変更が必要か
を検討することです。
システムへの影響がなく重要度も低いアイテムに対しては、 故障や劣化が発生してから対応
(リアクティブメンテナンス)する ことも含め検討します。 更に、故障メカニズムが判って
いても、これを制御できなければ、 再設計も含め検討する必要があります。
以上を体系的に実施することにより、
・リアクティブメンテナンス
・時間基準保全(TBM)
・状態基準保全(CBM)
・プロアクティブメンテナンス(原因除去型保全)
の組み合わせを最適化し、
・信頼度を最大化しつつ
・LCCを最小化する
ことを目指します。
検討に際しては、アイテムの潜在的故障やシステムへの影響を 体系的に検討するために、
FMEA(故障モードおよび影響分析)や FMECA(故障モードと影響および致命度分析)を
用います。
4.CMMS/EAMへの展開と連携
前置きが長くなりましたが、 本題のCMMS/EAMへRCMの検討過程や結果をどの様に反映し
ていくかを検討します。 本節以降では、時間基準保全(以後、単に予防保全と記す)の有効
性の検討を例に、 CMMS/EAM連携を説明します。
FMEAなどを実施し、 対象となるアイテムとその故障モードやシステムへの影響が判ってい
る場合、 何れのメンテナンス方式を採用するかが次の課題となります。
この時、対象となるアイテムが、CMMS/EAM中の設備台帳に記載されており、 メンテナン
ス履歴の抽出が可能であれば、検討実施時の故障確率を用いた評価に役に立ちます。 また、
既存設備の場合、対象アイテムに対する予防保全や 事後保全時の標準化された手続きが
(CMMS/EAM中に)存在すれば、 重要な、参考資料になります。
以下に、検討手順例を示します。
故障モードの発生原因の検討(複数存在するかもしれません)
各原因に対して、発生確率を抑えるまたはシステムへの影響を 許容できる範囲まで軽減することを検討します。
・利用中の設備の場合、対象アイテムについて故障履歴の抽出
・新規設備の場合、予想寿命入手や同機種、同環境での故障履歴の抽出
・故障発生時の処置と必要な費用の洗出し
・予防保全実施時の効果の評価と実施に必要な費用の洗出し
・検査実施時の効果の評価と必要な費用の洗出し
・状態監視実施時の効果の評価とモニター設置および維持のための費用の洗出し
・何れの方式でも、発生する影響(リスク)を許容できない場合、再設計
以上の情報から、それぞれのメンテナンス方式採用時の故障確率と 生涯コストを比較検討し
ます。
目標とする信頼性の確保を前提に、コストが最小化されるメンテナンス方式を選択し、 その
内容をCMMS/EAMに登録します。CMMS/EAMでは、予防保全や作業標準として活用されます。
5.具体例
次に、予防保全を例として、故障確率を評価しながら、 費用を最小化するための検討の例を
示します(コストミニマムの検討)(※3)。
※3 補足説明:
本検討では、コストミニマムを目的関数としていますが、 稼働率(非稼働率)を目
的関数とすることで、 稼働率(非稼働率)を最大化(最小化)する周期を 決定する
ことができます。 稼働率を用いて評価する場合は、稼働率目標を設定し、 検討する
のが現実的と考えられます。
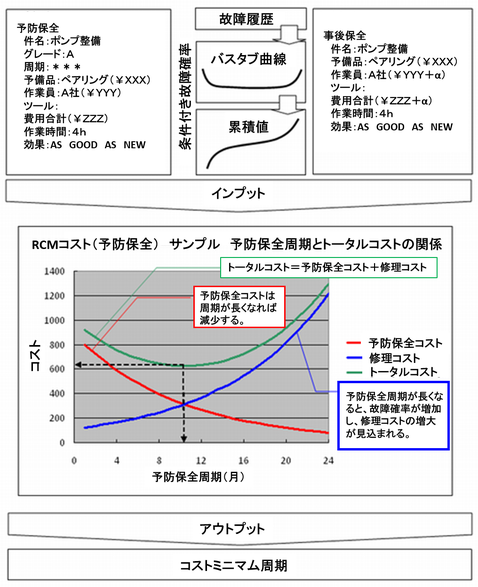
図3 RCMコストの例
アイテムの特定の故障に対する履歴 (上図では、バスタブ曲線)がわかっている場合、ワイ
ブル近似など(※4)を 用いて、経年による故障率の変化(故障率分布とよぶ)を算出する
ことができます。
経年による故障確率が判っている場合、 修理の発生確率や時間基準保全(上図では、予防保
全と表記)の回数(周期)から アイテム維持のためのトータルコスト(生涯コスト)を計算
することができます。
上図の例は、アイテム維持のためのトータルコストと予防保全周期の関係を 示したもので
す。
予防保全周期を長くしていくと、予防保全コストは、 減少していきますが、故障の確率が高
くなるため、 修理コストが増大することを表しています。 予防保全コストと修理コストを足
したトータルコストには、 ミニマムコストが存在することを示しています。
※4 補足説明:
故障履歴が存在する場合は、ワイブル近似などを用いて、 履歴から故障特性を求める
ことができます。 バスタブ曲線のように、初期、ランダム、磨耗故障と時期が分かれ
ている場合は、 3つのフェーズにわけ、ワイブル近似を適用します。 故障履歴が存在
しない場合は、ワイベイズ関数や、ベイズ統計、または、信頼度予測モデルを 用いて
故障確率分布や故障確率を推定します。
次に、「検査や状態監視を実施する場合でも、予防保全が必要か」を検討するため 検査や状態監視の有効性を検討します。検査や状態監視を実施する場合は、 劣化曲線を考え、P-Fインターバル中に、故障の兆候を検知できるかを検討します。 以下に、回転機のベアリングの場合の劣化曲線の例を示します。
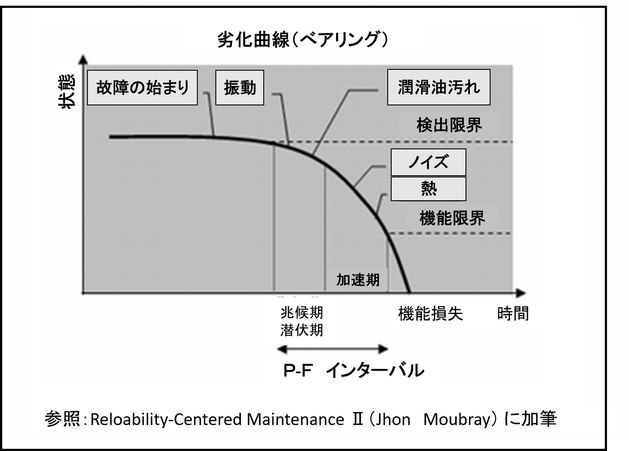
図4 劣化曲線の例
検査の有効性を検討する場合は、
・P-Fインターバル期間中に、検出可能か
・もし、1回目の検査で、検出できなかった場合でも、次回の検査で、検出可能か
・その時の周期はどれだけか
・検査実施の費用は、どれだけか
・停止時間が、どれだけか
などを検討します。
モニター装置などで状態監視を実施する場合は、
・対象となる故障モードを検出可能か
・検出可能な場合、その確率は、どれだけか
・検出後のタスクは、何か
・モニター装置の設置費用や維持費は、どれだけか
などを検討します。
もし、モニター装置などによる状態監視により、 故障の予兆検出が100%可能とする場合、
故障してから(被害が発生してから)修理ではなく、故障する前に計画的に対処することが可
能となります。状態監視を実施していることにより、予防保全や検査の頻度を減らせることを
示しています。予防保全周期や検査周期を大きくとるほど、トータルコストは、 低くなりま
す。すなわち、予防保全や検査は、その頻度を少なくしても良いと判断できます。但し、予防
保全や検査には他の目的も含まれていることには留意すべきです。(※5)。
モニター装置が対応できない故障モードが存在する場合、故障の予兆検出は、 100%では、な
くなります。 この場合は、他の保全方式との組み合わせが必要になってきます(例えば検査など)。
※5 補足説明:
故障の予兆を検出した後、フォローアップ処置が 発生する場合、本費用を考慮する必
要があります。 通常は、直近の計画作業が存在する場合、その中で一括して実施する
と考えられます。
以上の検討を、CMMS/EAMの設備階層上で検討すると以下の とおりとなります。
例を下図に示します。
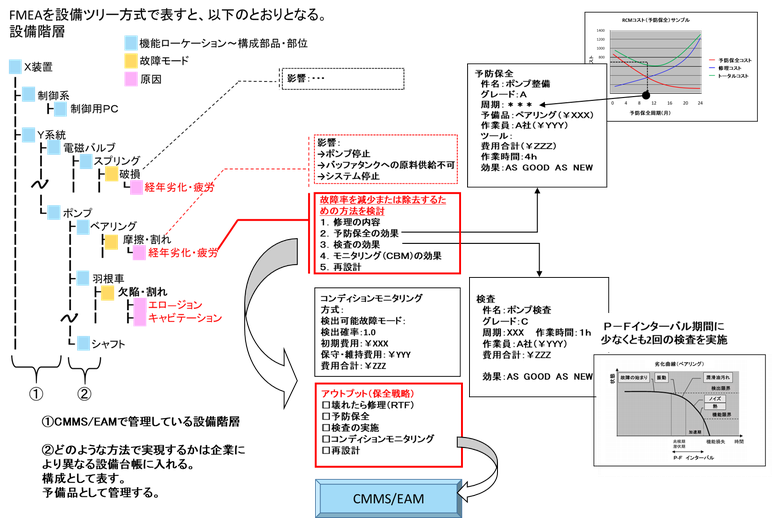
図5 設備階層とRCMコスト
上図は、FMEAを直感的に捉えるために、アイテムまでを設備階層で表しています。
階層末端は、部位や部品です。 末端の故障は、上位の故障を引き起こし、システムへ影響を与
えます。 階層末端には、末端のアイテム(機能)、故障(故障モード)、故障時の影響、およ
び、 その原因が示されています。 各故障について、対策を検討します。
検討の結果、採用されたメンテナンス方式は、CMMS/EAMの予防保全や作業標準として登録
します。 CMMS/EAMの以下の情報を書き換えることになります。
・根拠・理由(検討結果を設備や標準作業、予防保全に添付)
・故障の状況、処置、原因(要因)、対策
・標準作業(標準的な作業や検査の内容、タスク、予備品、ツール、コスト)
・予防保全とその周期(標準作業を参照)
・検査とその周期(標準作業を参照)
・設備階層の更新(予防保全や作業標準の対象部位や部品が増えた場合)
・設備の重要度やランク
上図の故障モードや原因は、CMMS/EAMの状況、処置、原因(要因)、対策などの 事後保全報告に使用する故障コード群として実装します(※6)。
※6 補足説明:
故障コードは、どのレベルまでを載せるかを十分検討しておく 必要があります。
故障の原因には、物理的根本原因、 人的根本原因(ヒューマンエラー)、潜在的根本
原因が含まれています。 FMEAによる評価結果から原因および要因をコード化して登
録することで、 根本原因や恒久対策の精度を上げることができます。
下図に、根本原因の階層構造を示すために、RCA(根本原因分析)のコンセプトを示
しておきます。
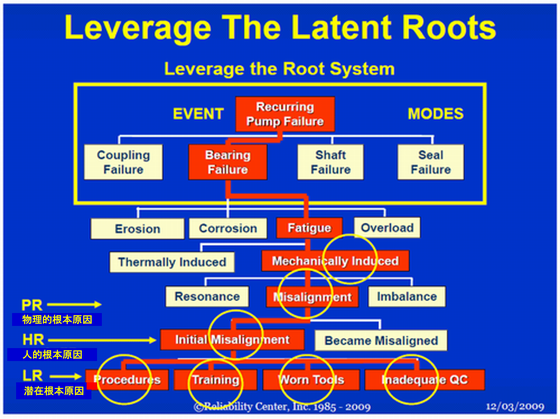
☆本資料は、故障テンプレート付きRCAツールPROACT(r)のコンセプトを示すものであり、Reliability
Center Inc.社のご好意により掲載しています。
図6 RCAのコンセプト
6.最後に
信頼性中心保全では、全体の評価を実施する中で、 重要なアイテムを絞りこみ実施することが
必要ですが、 その時、利用するツールであるFMEAは、ボトムアップ方式の検討方法を提供し
ます。 FMEAのみで、プラント全体を評価する場合、いつ終了するのか、 費用は、どれだけ必
要なのか見積りが困難になります。 重箱の隅を突っつくようなものであるため、 検討漏れに対
する不安や全体の把握困難が発生します。
現実的には、信頼性ブロック図分析のような全体の信頼度を見渡せるような評価方法や フォー
ルトツリー分析のようなトップダウン方式の併用による信頼性評価の実施、 または、リスク評
価を実施し、重要な機器を十分に絞り込んだ上での実施が 必要となります。
また、対象アイテムの各故障を評価し戦略を決定していく中で、同様の対策方法や、 周期の異
なる同一タスクが多数出現します。実際には、法令点検など、予め決まったタスクを考慮し、
検討していく必要があります。更に、CMMS/EAMと連携して用いる場合は、これらをグルー
プ化し、 計画作業や作業標準としてまとめる作業が必要になります (これをWork Package
と呼びます)。
次回以後のメルマガにて、トップダウン方式を用いたシステムの 信頼性評価とCMMS/EAMの
関係、タスクのグループ化とCMMS/EAMの関係を検討します。
次 「第10回:システム(系や系統)の評価とCMMS/EAMによる管理」
<お問い合わせフォーム>
● お問合せ先
株式会社ウェーブフロント
営業部
メール:sales@wavefront.co.jp
TEL:045-682-7070